What is Six Sigma?
Six Sigma is a management methodology comprised of tools and techniques that allow the improvement of business and manufacturing processes as well as the reduced variability in these processes through the use of statistical analysis. It is a highly disciplined, data-driven approach and methodology that has the central objective of achieving measurable and quantifiable financial returns.

Why Do Organizations Need Six Sigma?
Six Sigma was developed by Motorola in the 1980s and has since then come a long way to be accepted and adopted in a wide range of industry verticals. Today, Six Sigma certifications and knowledge are highly recognized and acknowledged for their ability to reduce defects in business and manufacturing processes. Professionals that want to build their career in management will definitely benefit from acquiring six sigma green belt certification online.
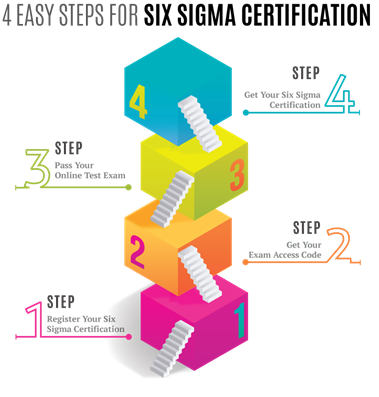
Some of the benefits and reasons why organizations need and use Six Sigma include the following:
Improved efficiency: Its single-minded focus on the reduction of defects and material waste leads to an increase in business/organization productivity with the same amount of resources. Waste is described as anything that does not enable the production of products and services required by a customer.

Minimized costs: A reduction in defects in processes also lead to diminished expenses because fewer materials and time are used to produce an equal or greater amount of output.
Revenue increase: Since Six Sigma processes are streamlined so that inputs (e.g., materials, time, etc.) and outputs are optimized, the result is that more revenue is made because productivity and efficiency are enhanced while costs are minimized.
Efficient process mapping: Six Sigma utilizes process mapping which enables organizations to document specific business processes through flowcharting. The mapping/flowcharting process is useful for making significant improvements towards upgrading operations, better utilization of resources, and higher productivity.
Continuous improvements: Organizations with Six Sigma professionals have the capability (skills and tools) to identify bottlenecks/problems/challenges that lower performance, and production which in turn allows the organization to identify areas that can be improved. As such, the quality of processes and products/outputs are continuously enhanced.

Top 7 Challenges Businesses Face Deploying Six Sigma Initiatives
Although Six Sigma brings a lot of benefits and enhanced management to organizations, there are still some challenges that need to be overcome. Almost all of these challenges can be easily overcome through good training of Six Sigma professionals as well as proper implementation and dedication to the Six Sigma process.
The top challenges that mainly arise with Six Sigma implementation usually come from the people involved and how the methodology is applied. Below are the top seven challenges that businesses face when deploying Six Sigma initiatives.
People-related challenges
When Lean or Six Sigma is applied, there is no room for feelings in the equation. Essentially, any process can be measured, analyzed and improved upon. If any waste is found, then a plan must be put into action to not only eliminate the waste but also to sustain and enhance upon the changes. It, therefore, goes without saying that individuals need to be onboard, or at least made to understand the process. With this in mind, some of the people-related challenges faced when deploying Six Sigma include the following.
1. Improper training
Without in-depth training on the Six Sigma methodology, the application of the rules is not achieved with the necessary attention to detail. As a result, poor deployment and implementation leading to failure may be a direct consequence of improper training.
2. Weak support from management
If management isn’t convinced about the direct benefits of Six Sigma, or if its benefits are not achieved within a reasonable period, then a loss of interest naturally occurs. The loss of attention often leads to the waning of the long-term commitment and support from management required to succeed with Six Sigma.
3. Resistance to change
When the people involved (managers and other staff) are resistant to change due to entrenched habits, and worse yet, if their habits are inefficient, it can be difficult to succeed with Six Sigma. For example, people sometimes fear to lose their jobs. Nevertheless, the fact remains that Six Sigma focuses on eliminating waste and fixing defects and not on putting people out of work.
4. Lack of passion and dedication
Even if the actors involved in the change process understand it from a logical perspective, they may not always come to terms with the possible change from an emotional standpoint. In essence, there is little doubt that some apprehension will still manifest in one way or the other. When this happens, there may be some reservations in deploying and implementing Six Sigma with the required dedication and passion.
Implementation-related challenges
5. Scope creep
More often than not, organizations accurately define the right set of parameters and the ultimate goal that they seek to achieve when deploying Six Sigma projects. However, as new issues are uncovered during implementation, initial parameters and the ultimate goal often gets blurred, leading to scope creep. When this happens, the process is side-tracked and, it, therefore, becomes increasingly difficult to achieve the results that were initially envisioned.
6. Ignoring a data-driven approach
Collecting the right data, analyzing it and uncovering insights that will benefit the organization is a guiding principle in Six Sigma. When individuals/management decide that the data is not better than their instinct or when management doesn’t understand or follow the data-driven approach as they should, then the entire Six Sigma process is compromised from the get-go.
7. Lack of resources
When management is not fully committed to the process, the result is often that the resources required to accomplish the goal will not be provided. Even if management is convinced to offer what is needed eventually, the waste in time and effort will generally compromise the Six Sigma process.
The Bottom Line: Overcoming The Challenges
Like any other management methodology, an understanding of the Six Sigma methodology will be required which can be obtained by answering the six sigma questions for better people-skills, and a strong work ethic. If you want to succeed with your Six Sigma deployments, then it is necessary to ensure that there is clarity of goals and expectations throughout the organization. Also, the goals and expectations need to be realistic and achievable.
Furthermore, thorough the knowledge and understanding of Six Sigma before deployment and implementation is necessary. The essential tools and skillset are obligatory for application of the right approach towards solving the organization’s specific challenges or addressing particular needs.